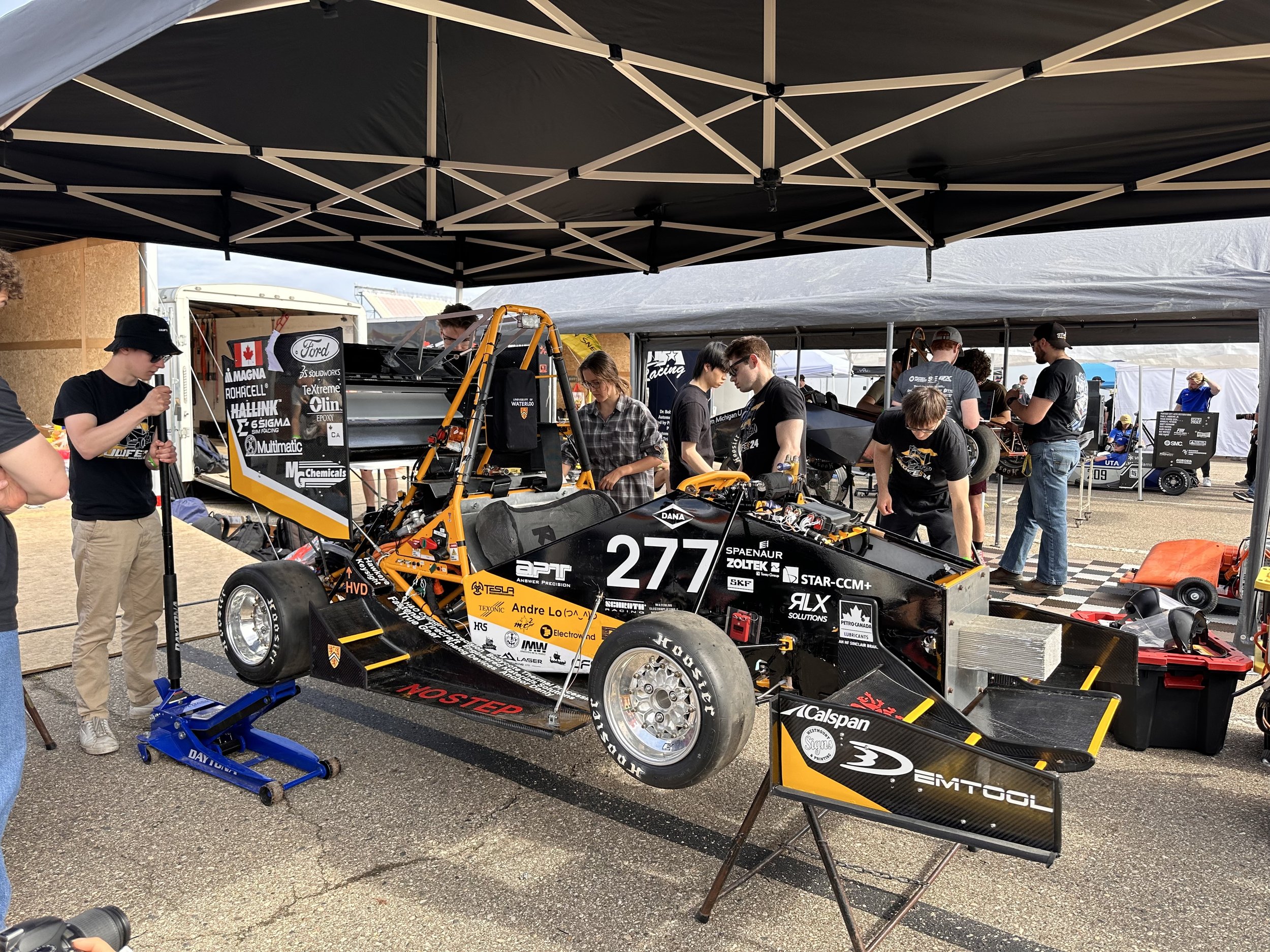
AERODYNAMICS
In a similar concept where planes rely upon the aerodynamic effect to fly, motorsport vehicles flip the wings of planes upside down, pushing tires into the ground. The increase in friction is directly proportional to faster cornering and better lap time. The Aero team of UWFE endeavors the pursuit for a delicate balance between downforce and resulting drag by utilizing advanced tools such as CFD alongside wind tunnel opportunities.
BUSINESS
The business team manages a multitude of functions. Apart from managing the team's finances, building funding proposals and liaising with sponsors, this sub-system is also responsible for member recruitment as well as the upkeep of social media channels and the website. By strategically building partnerships and associations, the business team aims to support our technical subsystems with funds for material, equipment, and professional contacts. In all, they seek to maintain a healthy inflow of support, ensuring brilliant ideas transform into reality. They are why the team continues to exist, and success in the competition is unlikely without a strong business team behind the scenes.
CHASSIS
The Chassis team is responsible for the base structural framework of the car onto which all other systems mount, as well as the braking system, firewalls, and impact attenuators. More importantly, It performs the carrier role for various load transfers, such as ensuring minimal deflection while enduring suspension compression. The chassis team strives to find the balance between rigidity and weight reduction; rigidity decreases uncertainty during energy transfer, improving efficiency. On the other hand, shaving weight in areas with fewer rigidity requirements simultaneously enhances power-to-weight efficiency. Deriving from the above, chassis development is closely tied with communication to other systems to understand supporting requisites and play a central role in making the concepts of other systems work efficaciously.
DRIVELINE
The driveline team is responsible for designing and manufacturing the components which move the vehicle forward. This includes a custom limited-slip differential which receives power through a chain from the electric motor. The driveline team also designs the cooling system for the motor and motor controller to keep these components at their optimal temperatures. Significant effort is put into improving the system's efficiency of converting electrical power from the battery, to useful mechanical power at the wheels. The driveline team is primarily focused on: mechanical design, thermal/fluid simulations and full vehicle simulations.
ELECTRICAL
Electronics resemble the brain and nervous system of our vehicle. However, unlike the human body, which has one central processing unit for all incoming signals, our electrical architecture adopted multi-control boards set up, each responsible for one major vehicle segment. The advantages of this approach contribute from shorter wiring from sensors to control units, minimizing voltage drops and electrical noise hence yielding higher precision and faster processing rate. Taking the battery pack ( accumulator) management segment as an example, we have individual boards for each segment, taking in cell voltage and temperature data, then transferring information to a battery management unit board that analyzes the data and return instructions to monitor, charge, discharge and balance our custom battery pack.
FIRMWARE
The firmware team manages the direct software linkage towards and between electronic control units facilitating all incoming signals and returning the according responses. It resembles the nervous signals we rely upon receiving sensations and reactions to that exact input. However, unlike our human body, which conventionally only receives these signals in existing situations, it is uncommon for ECU to receive simulated inputs being voltages. In fact, that reveals another important attempt of the firmware sub-team: simulate situations, monitor signal paths, and test the functionality of various controlling boards. Their importance is laid out simply by their description, as any failure in this communication system would result in a significant performance decrease or even a DNF.
SUSPENSION
Every tenth of a second matters on the track! The suspension team is responsible for connecting the car to the track, and is involved all the way from high level conceptual design to fine tuning the car on track. Precision is of the essence when it comes to developing suspension kinematics, vehicle dynamics models, lightweight yet stiff components and combining them all to create a fast and nimble Formula SAE race car..
TRACTIVE
The tractive team is put in charge of designing, manufacturing and maintaining the High-Voltage battery of the vehicle. This year, effort is being put into designing a larger, more efficient high-voltage battery. We are increasing our pack energy from ~5kWh to ~9kWh while stepping up our pack voltage from 294V to 588V. Significant work is being put into: reliability/serviceability, safety and efficiency. The Waterloo Formula Electric HV battery has historically set the bar for professionalism, and we plan to continue this trend going forward. The Accumulator team is multidisciplinary, primarily focusing on: mechanical design, thermal/fluid simulations, HV (high-voltage) systems design and power electronics.